Library
From case studies, to white papers, technical articles, FAQs, potential problems and creative solutions
From the very general to the highly specific and everything in between — developed by our technical experts and talent across a host of industries, our Library is the place where you will find all you need to ensure success. It’s unique and part of the Croll Reynolds’ value proposition: an unwavering commitment to ensuring that your plant runs. And stays running. What’s best, we’re constantly adding new materials.
Corporate Brochures (all downloadable pdfs)
Product Bulletins (all downloadable pdfs)
Multilingual Resources
Download our corporate brochures in your preferred language:
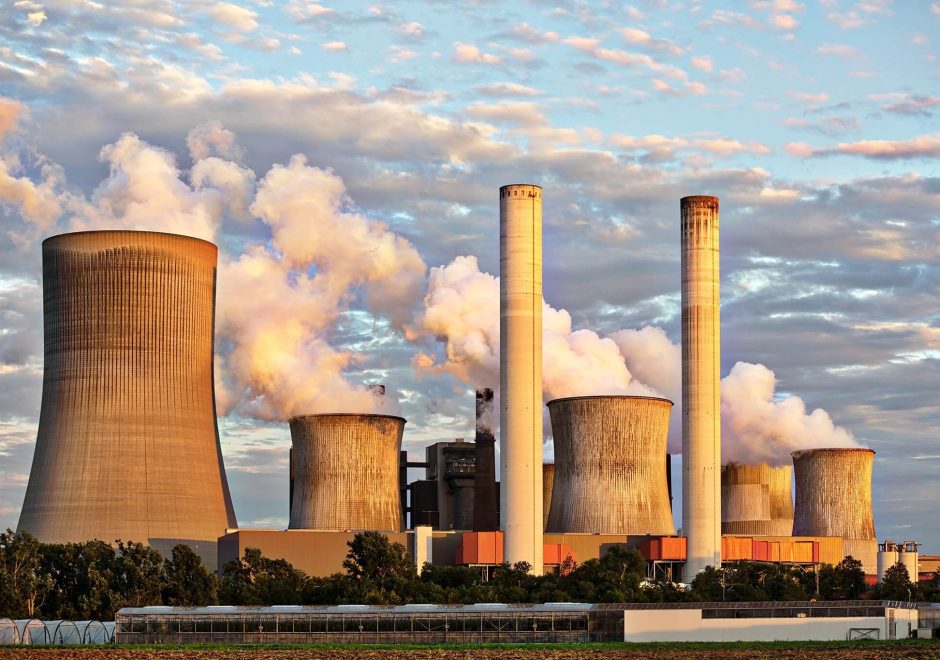
Ejector Technology:
Operation and Design Fundamentals
Videos/Infographics
Steam Ejectors
Steam ejectors use a motivating fluid and pressure-to-velocity energy conversion to create vacuum. Nozzles convert high-pressure steam to high-velocity steam in the mixing chamber to create a low-pressure region.
As the steam and entrained air travels down the diffuser, kinetic energy is lost and pressure increases again. Steam ejectors handle high volumes of gasses, including wet, corrosive, or particulate-laden vapors, and operate in the rough or medium vacuum range, with operating pressures to 0.003 torr. Multiple-nozzle designs, a Croll-Reynolds specialty, improve efficiency. Steam ejectors mount in any orientation and have a low maintenance design with no moving parts. Multi-stage systems offer improved vacuum, and can contain up to six ejector stages. The number of ejectors is determined by the level of vacuum required. Condensers are included to remove steam from the system and reduce load on later stages.
Shell and tube condensers, such as the one shown here, cool the steam down using arrays of cooling tubes. Condensate is drained from the system, allowing more steam to be added at the next ejector. Each system is a custom design and multiple condensers can be used as well. Steam ejector systems provide the lowest capital costs among vacuum process pumps.
To learn more about steam ejector systems and to discuss your specific vacuum process or application, contact Croll-Reynolds or visit www.croll.com.
Hybrid Vacuum Systems
Rotajector systems are high-efficiency combination ejector-liquid ring vacuum pump systems wherein the liquid ring pump replaces the final ejector stage of the system to reduce steam consumption.
Rotajectors are highly reliable, with only one moving part. They handle a wide range of gasses,vapors, particulates and contaminants without the need for filters separators or traps.
The process gases to be handled by the Rotajector system are drawn in through the suction inlet of the first stage ejector and compressed by the ejector stage(s) to an inter-stage condenser.
The interstage condenser cools the gases and condenses the vapors, reducing the load to be handled by the liquid ring vacuum pump. The liquid ring vacuum pump serves as the final compression stage. The condensate from the interstage condenser drains directly into the pump suction port. Pressurized steam is required for operation of the ejector stages and a continuous flow of sealant water and electrical power is required for operation of the liquid ring pump.
The liquid ring vacuum pump is designed to replace replace the final ejector stage(s), thus reducing steam consumption.
Rotajectors can be installed at ground level eliminating the need for barometric condensate piping.
Rotajectors can be operated using low pressure steam, eliminating the need for high-pressure boilers.
Each rotajector system is custom designed, with the liquid ring vacuum pump size optimized to match the ejector design.
To learn more about high-efficiency rotajector systems, and to discuss your specific process or application, contact the Croll Reynolds vacuum engineer in your area or call our US offices to speak with our design engineers.
Thermocompressors
Croll Reynolds Thermocompressors are designed to recycle heat energy by capturing and recompressing waste steam for use elsewhere.
Thermocompressors, like ejectors, have no moving parts. The mechanical design consists of a steam chest, nozzle holder, nozzles, and diffuser.
The thermocompressor uses high pressure steam, as a motive fluid, which enters the steam chest and expands through the nozzle.
The high-velocity steam then entrains the waste steam, into a mixing chamber where the fluids are combined.
The mixed fluids are then recompressed to an immediate pressure through the diffuser, which acts as a nozzle in reverse, reconverting velocity energy to pressure energy.
Thermocompressors are designed for applications in the food, petroleum, chemical, power, and paper industries. Thermal recompression is typically applied in the dairy and juice industries to recapture and reuse steam from evaporators during the concentration process.
All Croll Reynolds thermocompressors are custom designed and performance tested to meet our client’s exacting specifications.
To learn more about Croll Reynolds thermocompressor heat recovery systems, and to discuss your specific process or application, contact the Croll Reynolds vacuum engineer in your area or call our US offices to speak with our design engineers.
Steam Ejector
Steam jet ejectors offer a simple, reliable, low-cost way to produce vacuum. They are especially effective in the chemical industry where an on-site supply of the high-pressure motive gas is available.
Ejectors are considered an alternative to mechanical vacuum pumps for a number of reasons:
- No source of power is required other than the motive gas;
- Because they have no moving parts, they are reliable vacuum producers;
- They are easy to install, operate and maintain.
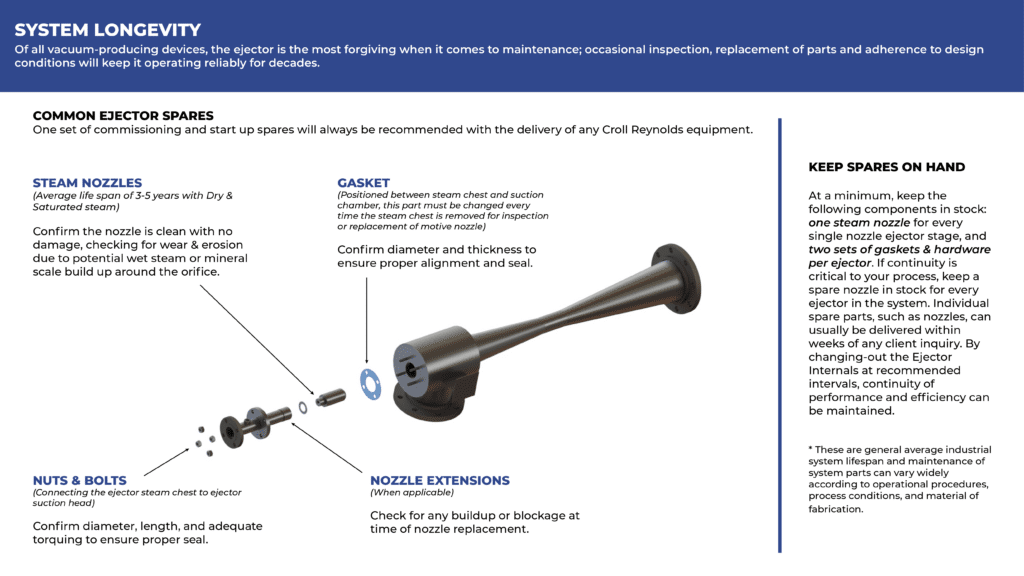
Case Studies
For your vacuum system requirements, contact our US headquarters in Parsippany or our representative offices in your area.