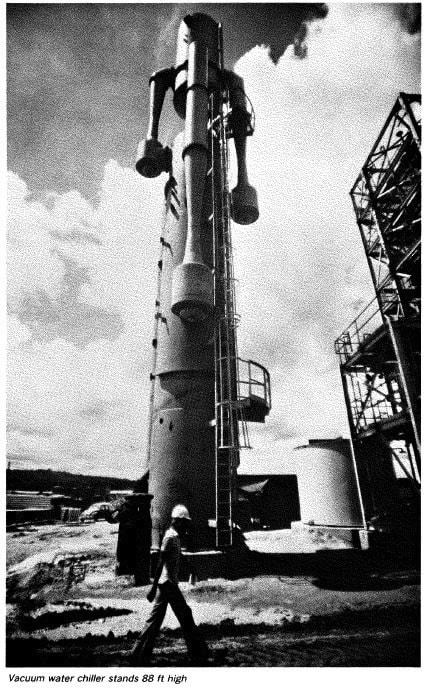
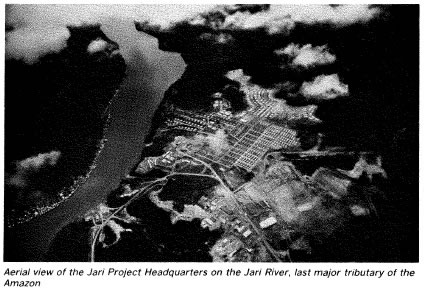
Reducing the consumption of resources and increasing system performance are top priorities in
The requirement for economical and efficient operating solutions in the oil and gas
Croll Reynolds Company, Inc. is a US-based engineering firm specializing in the design, and manufacture of process vacuum systems and related equipment.
Subscribe to our newsletter to get the latest updates and information on our business.