Vacuum Chillers
Vacuum Chillers
Chemical-free refrigeration and flash cooling applications
About Vacuum Chillers
Croll Reynolds vacuum water chillers are a low cost-solution to cooling high volumes of water for the chemical, pharmaceutical, food and paper industries. This vacuum pump chiller uses our multi-nozzle ejector technology in multiple stages to draw vacuum on various chambers of a chiller tower and gradually cool down the required flow of water to 1.5° – 10° C depending on the starting temperature of supplied water. Croll Reynolds vacuum chiller systems incorporate two to five multi-nozzle ejectors a chill tank with internal weirs, downstream of which will always be a two-stage ejector (air pump), piping, controls, and instrumentation for easy and proper operation of the system.
With over 300 unitsonline worldwide, Croll Reynolds is recognized as a leading designer and industry supplier of vacuum chillers. Croll Reynolds has designed and constructed three of the world’s largest vacuum pump chillers for the chemical and petrochemical industries. This chiller vacuum pump has assorted applications; it can be used to chill sand and gravel during dam construction and support the careful processing and chilling of fresh produce, meat, and grain products.
Advantages
- No chemicals or refrigerants
- No absorption solutions or lubricants for operation
- lower operating costs
- Reliable, consistent service and output
- No moving parts
- Low initial cost (compared to mechanical pumps)
- Minimal maintenance cost (compared to mechanical pump)
- Easy to operate and maintain
- Easy to retrofit or upgrade
- Long lasting and durable equipment
- Can be constructed from a wide variety of steel, alloy, or high alloy
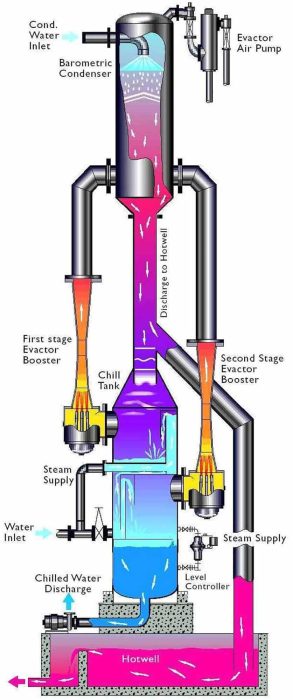
Croll Reynolds vacuum chillers use a multi-nozzle ejector technology to draw water through stages of the system, cooling it down as it moves through the system stages. The process begins with a two to five-stage ejector (air pump) that creates a vacuum in the first chamber of the chiller tower. This vacuum pump chiller draws water into the chamber and through internal weirs, where it then moves on to the next chamber. This process is repeated until the water has reached the desired temperature, typically between 1.5° – 10° C.
One of the main advantages of using vacuum chillers is that they do not require any chemicals or refrigerants, making them a more environmentally friendly option compared to traditional mechanical pumps. Vacuum chiller pumps have no moving parts, which results in lower operating and maintenance costs. They are also easy to operate and maintain, making them a reliable and consistent option for chemical-free refrigeration and flash cooling applications.
- Chemical –product distillation, drying, flash cooling and more
- Pharmaceuticals – controlled conditions for chemical processes
- Food and Beverage – product crystallization, evaporation and more
- Flavors and Fragrances– refinery processes, product degassing and more
- Pulp and Paper – product crystallization, evaporation and more