Desuperheater
Desuperheaters
Return steam to its optimal, saturated state for heat transfer applications
About Desuperheaters
Although process steam is typically throttled and superheated for efficient distribution, it must be cooled before it’s condensed because it’s less efficient than the saturated steam for many heat transfer operations. The most efficient way to reduce the temperature of superheated steam is to “desuperheat” it, by bringing superheated steam into direct contact with pressurized cooling water sprayed in form of small particles. This steam desuperheater mist of cooling water particles is dispersed using specially designed spray nozzles to maximize efficiency. The desuperheated steam is cooled through the evaporation of the water droplets and exchange of heat between steam and cooling water in a concurrent flow.
All Croll Reynolds’ steam desuperheaters are tailored to optimize the temperature reduction of superheated steam within your process. Nozzles are custom designed as with single, multi, or spindle-types nozzles to provide precise temperature control. The fine water atomization is also patterned to avoid side wall erosion. Croll Reynolds offers a full line of desuperheater heat pump configurations depending on the steam flowrates, turndown ratio, and available water pressure.
Advantages
- No chemicals or refrigerants
- No absorption solutions or lubricants for operation
- lower operating costs
- Reliable, consistent service and output
- No moving parts
- Low initial cost (compared to mechanical pumps)
- Minimal maintenance cost (compared to mechanical pump)
- Easy to operate and maintain
- Easy to retrofit or upgrade
- Long lasting and durable equipment
- Can be constructed from a wide variety of steel, alloy, or high alloy
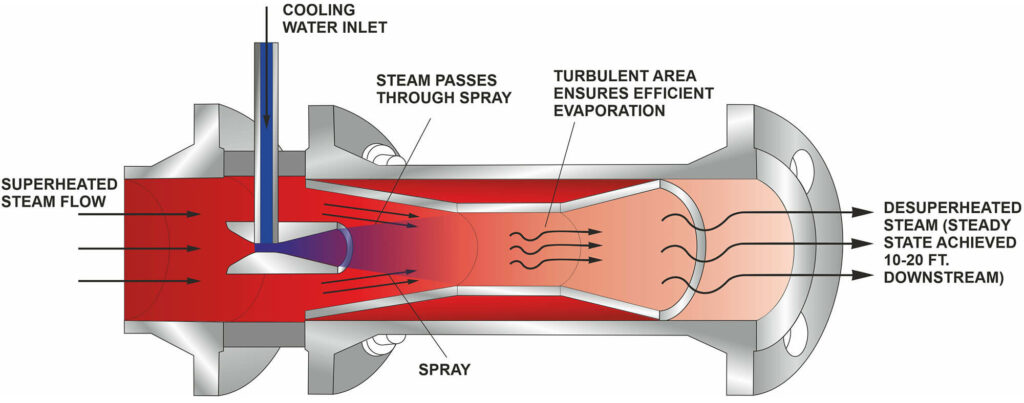
Superheated steam enters the venturi desuperheater at certain velocity range. A small fraction of the flowing steam enters the venturi in the desuperheater, speeds up to create a reduced-pressure zone into which spray water is drawn and atomized by steam energy, and then exits in a short expanding throat which allows pressure recovery. Cooling water enters the desuperheater nozzle at low velocity which forms a thin film. The dynamic energy of the desuperheater steam flow breaks the surface tension of the film since there is a very high differential velocity between steam and water which results in high shear and turbulence that are extremely effective in ensuring excellent desuperheating performance. The desuperheater venturi water nozzle, generally made in stainless steel, is a converging-stabilizing-diverging nozzle which promotes the turbulent mixing of atomized water and steam thus maximizing efficiency in a wide range of process conditions. Pressure drop on steam side is negligible. Water pressure at the inlet of the desuperheater should be at least 2 bar higher than steam inlet pressure
- Chemical –product distillation, drying, flash cooling and more
- Power Plants – removal of non-condensable gas for turbine efficiency
- Oil and Gas – refinery processes, product distillation and more
- Pulp and Paper – product crystallization, evaporation and more