Power Plant Vacuum System
Power Plant Vacuum System
Vacuum distillation for hydrocarbon recovery and processing
About
Croll Reynolds Steam Jet Ejector Vacuum Systems and Hybrid Ejector Vacuum System are utilized in coal, gas/oil-fired power plant as well as in nuclear and geothermal power installations. The efficiency of steam turbines in a power plant directly correlates to the pressure of the steam pressure exiting the turbine exhaust. A shell and tube condenser (Turbine Condenser) is typically installed to capture and condense steam exiting the turbine. Croll Reynolds vacuum systems installed at the turbine condenser’s outlet efficiently remove non-condensable vapors and the carried over water vapor from the turbine condenser and lowers the operating pressure of the condenser; this decrease of pressure at the turbine’s exhaust increases the amount of heat available for conversion to mechanical power by flow of high pressure, high temperature steam through the turbine blades.
Turbine bypass desuperheaters play a major role in power plant applications. Within a period of twenty-four hours, a Power Plant may be required to operate at minimum load, increase to maximum capacity for major part of the day, immediately cut back to minimum load and then back to maximum capacity. Bypass Systems permit unit-start up and unit-shutdown for critical heavy components in boilers and turbines. Bypass Valves are supplied with hydraulic, electric or pneumatic actuators as per the process requirements, along with complete control systems as an option.
The typical ejector vacuum system designed for power applications are two-stage, twin element units having duplicate ejectors for each stage; one element running and one element on standby. An additional, “Hogger,” start-up ejector is normally provided to evacuate the turbine condenser prior to turning on the primary two stage system (Holding system) to improve the evacuation time it could takes if Holding ejectors were utilized instead.
Advantages
These are the primary advantages of installing ejector vacuum systems for VDU packages:
- Lower operating costs
- Prevents hydrocarbon chains from breaking from undue, excessive heat
- Reduces other undesirable secondary reactions
- Increases product recovery (under maximum temperature constraints)
- Reliable, consistent service and output
- No moving parts
- Low initial cost (compared to mechanical pumps)
- Minimal maintenance cost (compared to mechanical pumps)
- Easy to operate and maintain
- Easy to retrofit or upgrade
- Long lasting and durable equipment
- Can be constructed from a wide variety of steel, alloy, high alloy, including corrosion resistant coatings of all components.
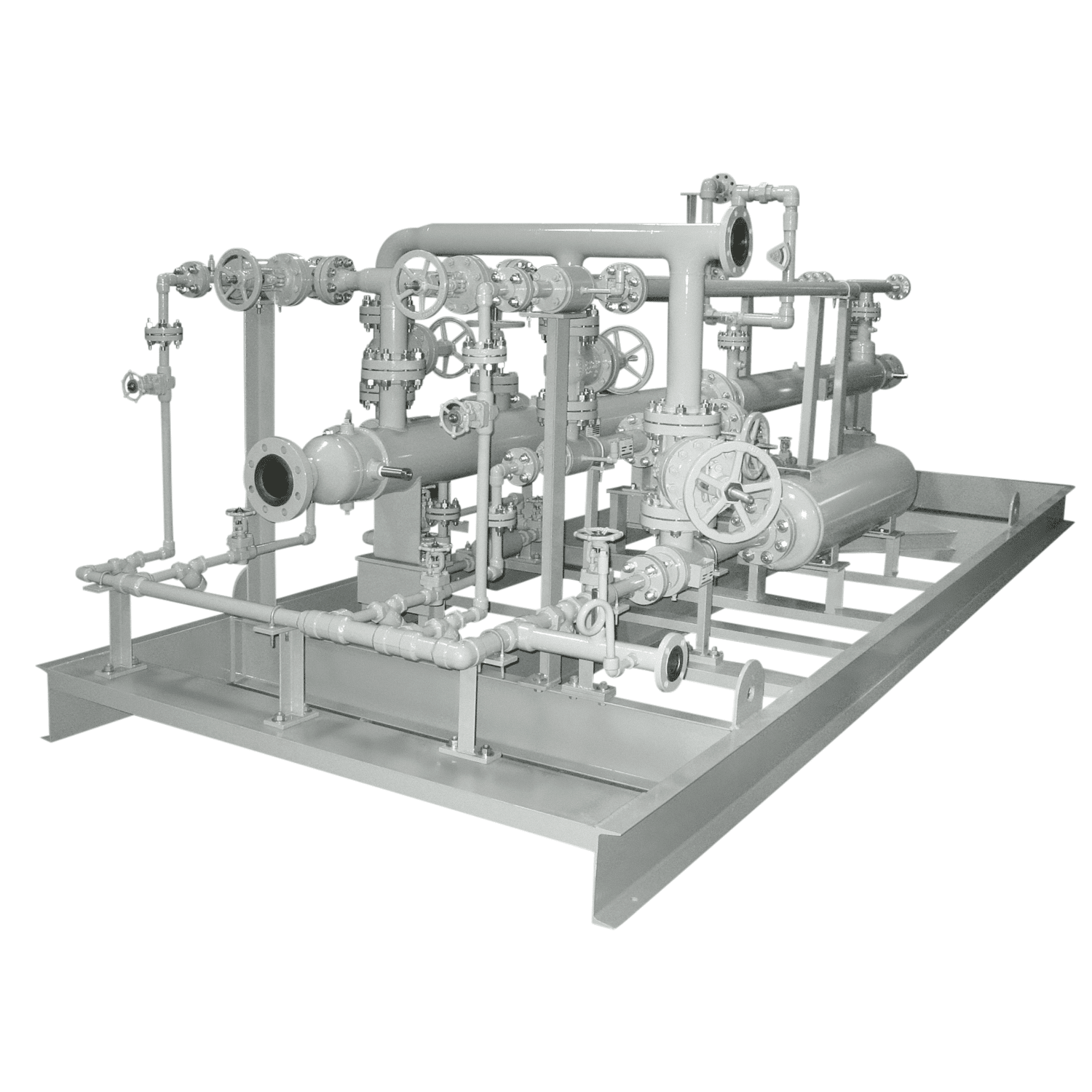
Vacuum distillation columns utilize vacuum system to achieve absolute pressure of 8 to 40 mmHg in the column using 2 to 4 stages of steam jet ejectors or a combination of steam ejectors and liquid ring vacuum pumps (Hybrid Ejector Vacuum System). The vacuum created in the column will be handled by usually large size 1st stage ejector, arranged with minimal interconnecting piping to reduce the pressure drop between the column and the vacuum system. Usually, the optimal number of stages for VDU systems with low-medium back pressure (≤ 0.3 bar G) are 3-stages of ejectors and condensers. The low pressure generated in the column will provide good vapor-liquid contact and achieve necessary pressure drop for the column. The vapor moving through the column condenses in distillation trays and then are withdrawn from the side of the column. For VDU systems with back pressure ≥ 0.3 bar G the system will be more efficient with 2 to 3 stage of steam jet ejectors with the addition of liquid ring vacuum pumps overcoming the high back pressures (up to 0.8 to 1.0 bar G).
- Power Plants – removal of non-condensable gas for turbine efficiency