Thermocompressor and Boosters
Thermocompressor and Boosters
Reliable Vacuum Service for the Process Industries
About
Thermocompressor are a form heat recovery equipment used to boost low-pressure steam to higher pressures for reuse in additional applications. This equipment maximizes energy efficiency by reclaiming the latent heat energy of a low-pressure steam; compressing the vapor load to meet higher pressure and temperature requirements.
Advantages
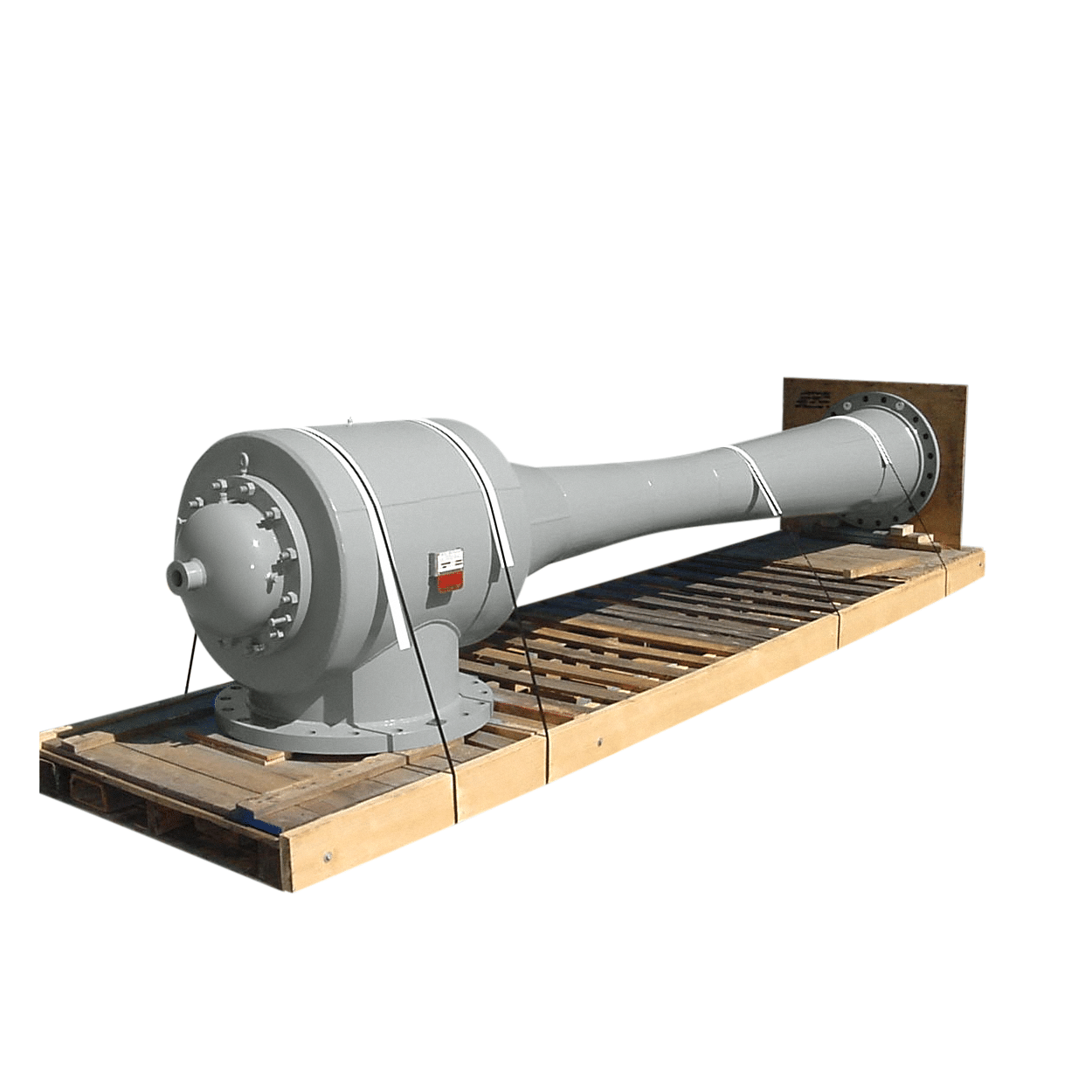
- Reliable, consistent service and output
- Handles high volumes of gasses and vapors
- Requires no electrical connections or external power (outside of motive steam)
- Low initial cost (compared to mechanical vapor recompressors)
- Can operate in very high-temperature applications
- Easy to install and maintain
- Easy to retrofit or upgrade
- Long-lasting and durable equipment
- Can be constructed from variety of steel, alloy, and composite materials
- Single or multi-nozzle design options
- Does not require lubricant, no wear-product interaction
-
No moving parts unless adapted for automatic controls
(spindle design options for turndown)
Thermocompressors take pressure energy of motive steam and convert it into kinetic energy (high velocity steam), which entrains and then compresses the low pressure spent steam, converting it back to pressure energy. The motive steam is piped into a steam chest and expanded through a converging-diverging nozzle. This high velocity steam entrains the steam entering the low-pressure steam into suction chamber and the mixed process and motive steam are then compressed to an intermediate pressure as they pass through the diffuser (throat). The diffuser acts as a nozzle in reverse, reconverting velocity energy to pressure energy.
The precise dimensions and arrangement of thermocompressors components are expertly engineered to govern velocity/pressure conversions. The diffuser’s geometry moderates the outflow conditions of the mixed stream to the end-state required by the process. Thermocompressors can be designed to achieve specific outlet conditions of mass flow rate and temperature or meet certain suction flow rates with specific suction and discharge pressures.
- Chemical –product distillation, drying, flash cooling and more
- Oil and Gas – refinery processes, product distillation and more
- Power Plants – removal of non-condensable gas for turbine efficiency
- Food and Beverage – product crystallization, evaporation and more
- Pulp and Paper – product crystallization, evaporation and more
- Water Treatment and Desalinization – product crystallization, evaporation and more