Three hybrid ejector/liquid-ring vacuum pump systems, operating on low-pressure steam process vacuum for a Milwaukee biotech manufacturer. When production runs are measured in kilograms, economic and reliable vacuum becomes more important than ever. Supplying reactors, ovens and evaporators, the hybrid systems handle heavy vapor loading.
Pharmacia P-L Biochemicals’ Milwaukee facility manufactures reagents for the biotech community: products like DNAs and nucleotides related to molecular cell biology.
Production scale is necessarily small for these high-tech materials. Much of the manufacturing is done on the lab bench. When it’s time to scale up a run – from hundreds of grams to kilograms or tens of kilograms – the work is moved into their pilot-plant sized manufacturing facility.
t’s in this pilot/production plant that vacuum was needed: for chemical reactors working under vacuum; for vacuum ovens; and for climbing-film evaporators. The vacuum systems selected were three “Rotajector®: hybrid systems composed of one or two ejectors and a liquid-ring vacuum pump. Conveniently skid-mounted, the systems were placed at various plant locations near the equipment to be supplied.
Why Use Vacuum?: A major production requirement for biochemicals is removal of water and solvents. It goes without saying that techniques of heating and boiling off excess water are out of the question when handling sensitive biochemicals. Reverse osmosis was a possibility but designers felt that traces of solvent would likely injure the membrane.
Rotary evaporation, used extensively on the bench, was the proven method. Pharmacia decided to scale it up for the pilot plant.
Vacuum Mandates Ejectors: Ejectors were considered the technology of choice and convenience for producing vacuum. However, the company’s previous units were designed for high pressure steam and did not fit into current requirements. Therefore, a low pressure steam source was considered so the problems associated with high pressure boilers would be eliminated. In addition, limited space and abbreviated room mandated a compact unit.
Hybrid Systems Solve Problems: Rotajectors can be skid mounted. In addition, their compact size permitted the ·smallest of the three systems to be shoehorned into a 2 1/2″ x 7′ long x 5′ high area. The Croll Reynolds’ design utilized a shell and tube intercondenser rather than the direct contact type. This feature eliminated process water contamination and the possibility of condensing water flashback into the process.
Best of all are the modest pressure requirements of the Rotajector.
Because the hybrid system incorporates a simple liquid-ring pump for the “rough vacuum” stage, pressure requirements for the ejector stages can be kept very low. Just 6 psig steam is needed for the PLB system.
Compared with mechanical vacuum pumps, the hybrid systems were the clear choice. Hybrids are “forgiving” systems. Neither trace solvents nor high purity water vapor loading would pose any problem to the ejectors or the liquid ring pumps, as may occur with oil-sealed mechanical vacuum pumps. Since the only moving part of a hybrid is the impeller of the liquid ring pump, (even this moving part involves no metal-to-metal contact with casing walls) operation and maintenance are simple and reliable.
Designing The Systems: At first a single large vacuum producer was considered. Because requirements of the vacuum-using equipment were quite different, it became clear that several systems, each optimized for the equipment served, would be preferable.
The large system serves several large climbing-film evaporators. Design conditions are 415 lb/hr water vapor plus I lb/hr at 0.5” HG abs. It utilizes two ejector stages and two shell-and-tube intercondensers.
The intermediate system serves a smaller evaporator and some evaporating ovens. Its conditions are 125 lb/hr water vapor and 5 lb/hr air at 0.5” Hg.
The small system is the vacuum source for a I 00 gallon and a 500 gallon reactor; its conditions are 28 lb/hr water vapor plus 7 lb/hr air at 0.5” Hg.
Both smaller systems use just one ejector stage and one condenser. All three systems operate on 6 psig steam, with 55°F inlet water for the shell-and-tube condensers.
Started in January, 1985, the vacuum equipment has been on-stream six years and is working as planned, providing reliable service while saving steam and water. Given the same conditions, company designers would make the same selections again and again.
Acknowledgements: Pharmacia P-L Biochemicals is part of Pharmacia Biosystems, an international company with head offices in Uppsala, Sweden and U.S. headquarters in Piscataway, NJ.
The three “Rotojector” hybrid ejector/ liquid ring vacuum systems were supplied by Croll Reynolds Co., Inc of Westfield, NJ. “Rotojector” is a trademark of Croll Reynolds.
About the Author: As Master Scheduler, Ted Hron plans production for this biochemical manufacturing facility. He has a headstart in this assignment: his previous position involved developing the same product structures and standards he uses now in planning.
By Ted Hron, Master Scheduler – Pharmacia P-L Biochemicals Inc., Milwaukee, WI
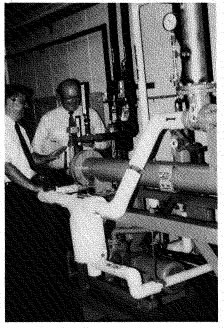
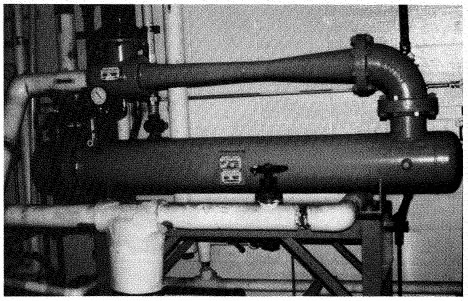