The Stepan Company, headquartered in Northfield, IL, is a major manufacturer of basic and intermediate chemicals with modern production facilities located in Illinois, California, Georgia, New Jersey and Grenoble, France. The extensive product line includes surfactants which are used to formulate personal care, household and industrial cleaning products, high purity ester emollients for pharmaceuticals and cosmetics, synthetic lubricants, emulsifiers for herbicides and pesticides, urethane foam systems for thermal insulation, and defoamers for the pulp and paper industry.
Stepan’s plant in Maywood, NJ has been producing some of the specialty chemicals. One of the buildings was equipped with several steam jet ejector systems as the vacuum source for various reactors and receivers. One three-stage and one four-stage system were dedicated to batch production of esters, and a larger three-stage system was used when making batches of other specialty chemicals and synthetic lubricants.
Shortly after Stepan acquired a Philadelphia chemical company in 1982, the Maywood plant was typically operating three shifts a day, seven days a week in order to meet production schedules. The three jet ejector systems were running at full capacity almost continuously, and the vacuum would be switched from one vessel to another as needed.
Another vacuum system and receiver had to be installed to share the existing load and to reduce the work week from seven to five days. The additional vacuum capacity would also be used to increase production of synthetic lubricants.
Solution: Maywood plant production and engineering personnel were satisfied with the performance and reliability of the steam jet ejector vacuum systems, but investigated other vacuum producers as an alternative. They decided that another three-stage jet ejector system was the most economical method for increasing vacuum capacity. The detailed study included energy costs to operate the system, evacuation or “pull down” time, and anticipated maintenance requirements.
The jet ejector is a relatively simple vacuum producer with a nozzle, mixing chamber and diffuser as the three basic components. A pressurized fluid such as steam is directed through the converging nozzle and the increase in velocity creates a vacuum in the mixing chamber. Material sucked into the chamber is entrained with the motivating fluid. The uniformly mixed stream travels through the diffuser at a velocity intermediate to the initial velocity of the motive fluid and suction fluid, regaining most of the pressure lost at the nozzle.
A jet ejector system may have as many as six stages. An intercondenser is usually installed in the system to condense the steam from the preceding stage and reduce the vapor compression load on the succeeding stage. Since an ejector has no moving parts, the only maintenance requirement is to periodically examine the nozzle and diffuser for wear or corrosion.
A three-stage jet ejector vacuum system, identical in design to the three-stage system which had been in service since 1969, was installed at the same location and elevation in the building. It is constructed of cast iron with stainless steel nozzles, has a lO” diameter surface condenser between the second and third stages, and produces a vacuum of 5 mm Hg.
Results: The Maywood plant was able to eliminate weekend production by installing another three-stage jet ejector system, and will remain on a five-day week at least until the capacity of the four systems is exceeded by production vacuum demands. A mechanical vacuum pump may then be installed in parallel with the third-stage ejector to provide additional pulldown capacity. The pump and all three stages would be used during startup to reduce evacuation time, which would speed up batch production. The pump would serve as the final stage when the desired vacuum for the reaction was achieved, and the third-stage ejector would be shut down to save steam.
By Paul Cunha, Plant Engineer, Stepan Co. with CP Staff
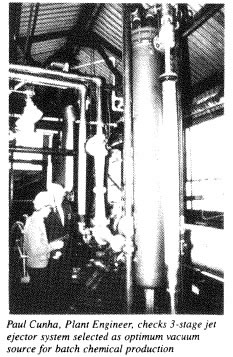