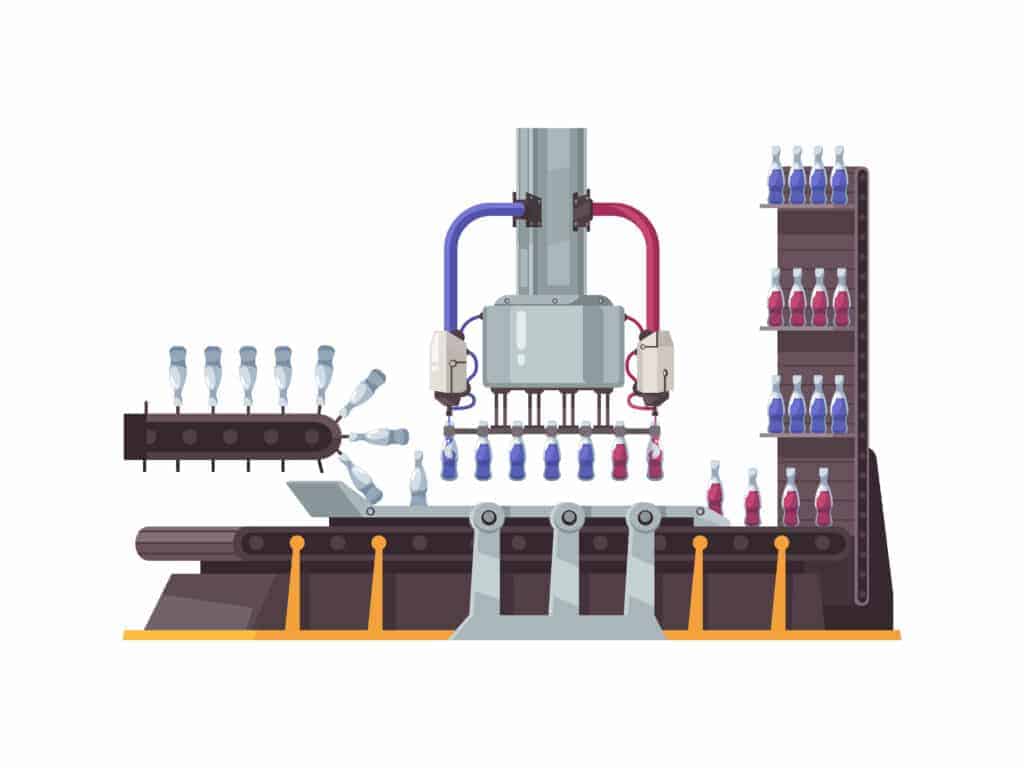
Do you want to know how steam ejectors or steam injectors work? Many industries today rely on these systems for their processes. Understanding the working principle of a steam ejector or steam injector system is important for the successful operation and maintenance of this equipment. In this blog post, we will discuss what a steam ejector is, its components, the intricate details of the working principle, and its benefits. If you’re interested in learning more about the power of such machinery and technology then read on. We will cover:
- Working Principle of a Steam Ejector or Steam Injector System.
- Functions of the Main Components.
- Advantages.
- Potential Issues and How to Fix Them.
- Choosing the Right Type of Steam Ejector or Steam Injector for Your Application.
- Preparation and Installation Tips.
Working Principle of a Steam Ejector or Steam Injector System
The principle of operation for a steam ejector or steam injector system is based on Bernoulli’s Principle. This states that when the velocity of a fluid increases, its pressure decreases. In simpler terms, it can be stated that a high-velocity jet of vaporized liquid (usually water) is used to “eject” or “inject” the product (usually gas) into the vessel. The steam ejector operates by utilizing the pressure energy from a motive fluid, converting it to velocity energy, and then ejecting this high-velocity jet of liquid into the vessel. The difference in pressure between the two sides creates a vacuum in the vessel, resulting in a flow of product through an outlet pipe and into another location.
Functions of the Main Components of a Steam Ejector or Steam Injector System
The main components of a steam ejector or steam injector system are the motive nozzle, diffuser, throat, suction chamber, and exhaust chamber. The motive nozzle is responsible for taking the input fluid (usually steam) at high pressure and transforming it into kinetic energy. This is done by constricting its cross-sectional area. The diffuser then directs the high-velocity jet of liquid and transmits it to the throat. Here, the pressure drops, and a vacuum is created which will cause the flow of product into the vessel. The suction chamber serves as an additional space to reduce turbulence while allowing for easier maintenance access. Finally, the exhaust chamber collects any remaining vapor/liquid mixture, ensures proper separation, and expels them out of the system back into their source mediums.
Advantages of Using a Steam Ejector or Steam Injector System
Using a steam ejector or steam injector system offers several advantages over other forms of machinery and technology.
- Firstly, they require minimal power consumption in order to operate – usually just one-third that of alternative systems such as centrifugal pumps or compressors.
- Secondly, they are incredibly efficient – with up to 95% of the motive energy being converted into useful output.
- Finally, they can be used in a variety of applications due to their versatility and ability to operate under a wide range of temperatures, pressures and flow rates.
Potential Issues with a Steam Ejector or Steam Injector System and How to Fix Them
Although steam ejectors or steam injectors may seem foolproof on paper, potential issues must be taken into account before installation begins.
Common problems include:
- Clogged nozzle tips from solid particles present in the input liquid or gas.
- Faulty seals that cause pressure drops or leaks.
- Incorrect sizing of the nozzles which will affect performance.
- Inadequate support for the piping system leads to ruptures/leaks.
- Poor maintenance leads to corrosion and erosion within the unit itself.
All possible solutions should be taken into account when selecting and installing a steam ejector or injector system.
Choosing the Right Type of Steam Ejector or Steam Injector for Your Application
When considering the installation of a steam ejector or injector system, it is important to determine the correct type for your application before making any further decisions.
Two main types are available: single-stage and multi-stage steam jet ejector systems. Single-stage units are used in smaller applications with lower flow rates and pressures while multi-stage units can handle more demanding conditions such as higher flows, temperatures, and/or pressures. Additionally, the material of construction must be selected in order to ensure that it can withstand any harsh operating conditions present at its location.
Preparation and Installation Tips Before Getting Started With Your New System
Lastly, there are some key preparation and installation tips that one should take into consideration when getting started:
- Make sure that the system is properly supported and braced.
- Ensure that all piping connections are secure in order to prevent any leaks or pressure drops.
- Inspect all components for signs of damage before switching on.
- Always follow the manufacturer’s instructions when it comes to operating, maintaining, and storing the unit.
By following these guidelines, a steam ejector or injector can be reliably used in numerous industrial applications and other scenarios where product transfer is required. By optimizing its design and installation process, one can ensure optimal performance, efficiency, and safety – making it an asset rather than a liability.
Get in touch with us
Related Posts
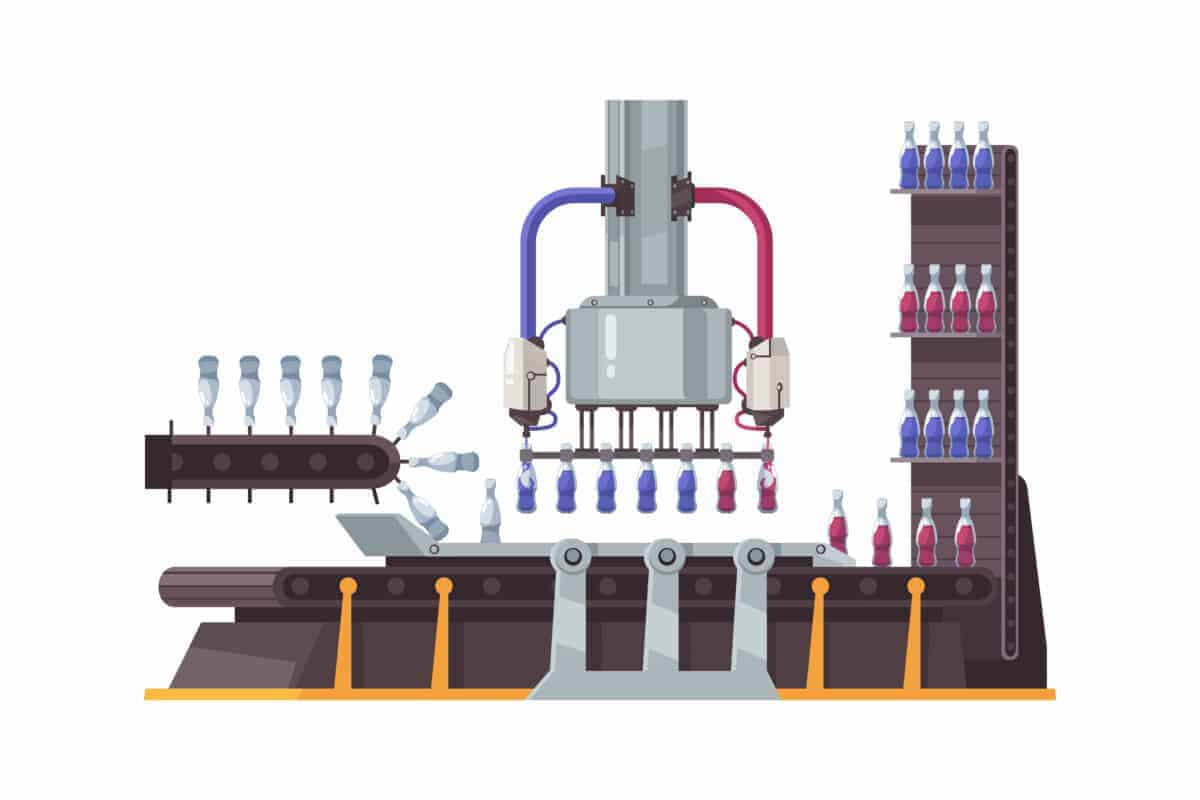
Understand the Working Principle of a Steam Ejector or Injector System
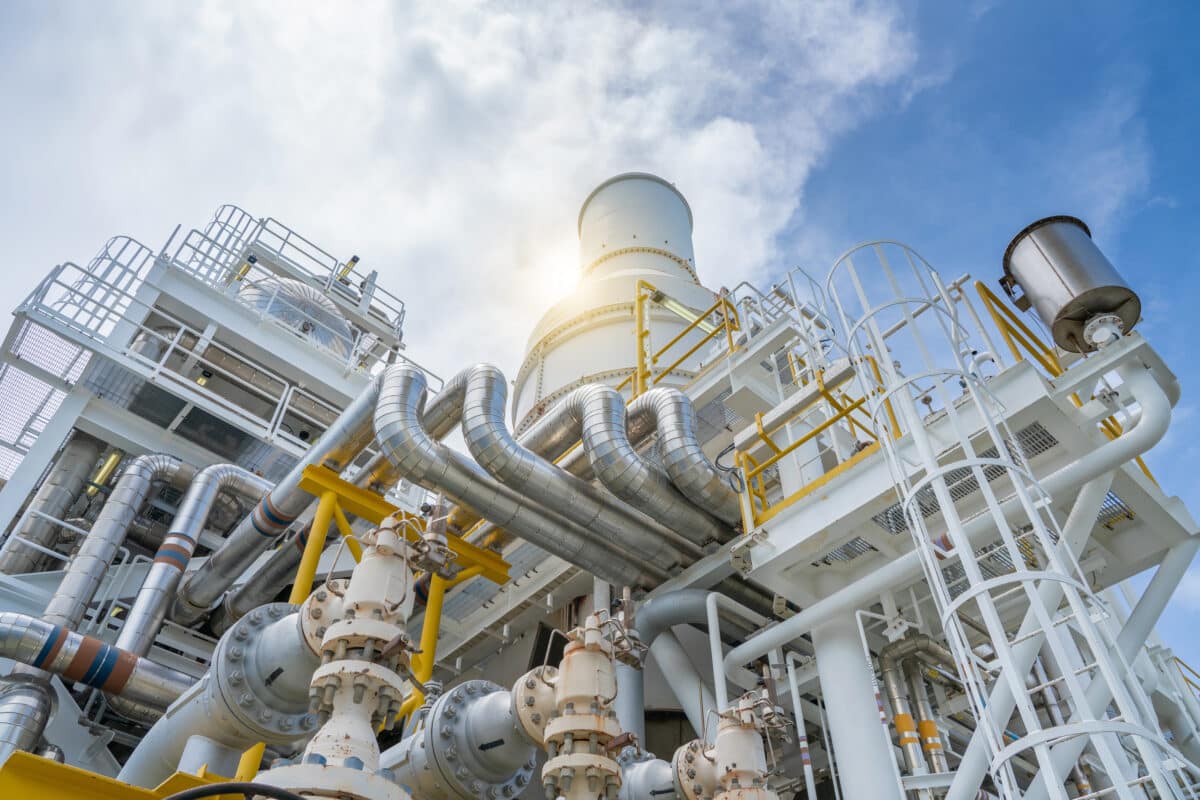
How Steam Ejectors Work: The Ultimate Guide
About Us
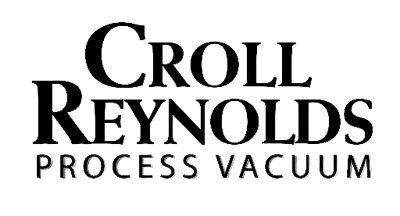
Croll Reynolds Company, Inc. is a US-based engineering firm specializing in the design, and manufacture of process vacuum systems and related equipment.