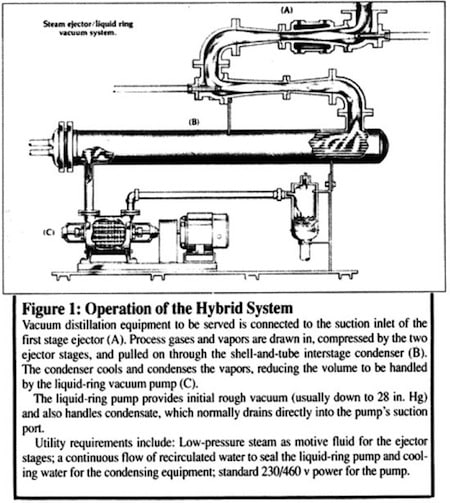
The Givaudan-Roure Clifton, NJ facility produces fragrance compounds , flavor compounds and specialty chemicals. Annual production runs to millions of pounds, but since the materials are varied and rare, most of this huge output is shipped in 55-gallon drums.
The processes are mostly batch type. Since many of the flavors, fragrances and specialty chemicals are time/temperature sensitive, they are purified at reduced temperatures by vacuum distillation. A very efficient vacuum process is desired in order to obtain the highest product yield.
Some 40 years ago, two steam-jet ejector vacuum distillation systems were installed in the chemical facility. One was a four-stage graphite ejector, serving two glass-lined vacuum distillation units involved with chlorides. The other was a stainless-steel ejector, serving multi-purpose batch distillation processes. This setup now required special treatment arrangements, as the two vacuum distillation processes were producing vapors and non-condensables containing toluene.
OCPSF (Federal Regulation 40-CFR, part 414.85) mandates that wastewater may contain no more than 28 ppb of toluene on average – a maximum of 74 ppb – and limits other priority pollutants that may be discharged to a municipal wastewater plant.
Proper treatment and disposal of wastes has always been an important priority for the company. The wastewater stripper system now being inaugurated for the two problem stills is designed to collect all traces of toluene and other pollutants for proper disposal. Latest in a long line of forward looking treatment arrangements, it aims at putting Givaudan-Roure in compliance with extremely tight Federal and state regulations.
Selecting New Vacuum Producers: To complement the new stripper system, it was decided to replace the 40-year old ejectors with the new vacuum producers to ensure reliable production of the required 1 mm Hg Abs vacuum. As the company saw it, there was choice of three methods of obtaining high vacuum: Mechanical vacuum pump, ejector vacuum system and hybrid system.
The mechanical vacuum pump was ruled out for fear of problems associated with mechanical devices used in high vacuum distillation service. There was concern that the complicated mechanism and materials of construction in a mechanical vacuum pump might not stand up to the fluids handled. In any event, Givaudan-Roure wished to retain the principle of steam ejector vacuum production as the most reliable source of the high vacuum needed. It was decided that the advantages of a steam jet/liquid ring combination system in the form of a Rotajector would address these concerns.
Economics of the new installation favored the hybrid system (see Figure 1). While two steam ejector stages would pull the final vacuum, rough vacuum would be provided by the energy-efficient liquid-ring pump. The cost of operation of the pump is significantly less than steam required for the two stages it replaces.
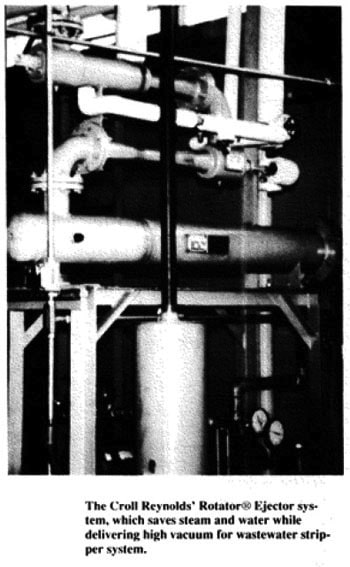
In addition to reducing steam consumption, the use of water is minimized. A liquid ring vacuum pump designed for full seal water recovery is also environmentally favorable. Condensed process load and motive steam make up a portion of the required sealant fluid of the pump, further reducing any fresh water needs. To remove the heat of compression and condensation, sealant is recirculated through a closed loop from the pump through a heat exchanger, a surge generator, and back to the pump.
Finalizing the New Installation: The older ejector systems were replaced with hybrid systems, installed in 1991 and 1992. Instead of the four ejector stages of the older systems, each has two ejector stages (graphite in one case, stainless steel in the other) plus a two-stage liquid ring pump.
Steam pressure at the main header is 300 psig reduced to 125 psig at the vacuum equipment. The systems are designed to handle 2 lbs./hr. @ 1 Torr. Where less vacuum is required, the liquid ring vacuum pump can be operated independently at vacuum levels of 50 Torr.
The hybrids are “Rotajector” systems supplied by Croll Reynolds Co., Inc., through the engineering assistance of AMSCO Engineering of Watchung, NJ. They were selected to match previous plant equipment. The company uses some 40 steam jet ejector systems in various areas of its Clifton plant, and most of this equipment is obtained from and serviced by Croll Reynolds.
By: Robert G. Watters, Plant Engineer, Givaudan-Roure Corporation, Clifton, NJ