A low-pressure steam jacket eliminates ice formation inside of a highNacuum (0.5-mm Hg) ejector. The jacket replaces multiple steam nozzles directed against the exterior of the first stage of the ejector. Untidy condensation and noise are reduced and stable ejector operation is assured.
The steam ejector system at Phillips Petroleum Co.’s Philtex/Ryton plant in Borger, TX, provides a reliable high-vacuum source for fractionation of heavy mercaptans. The continuous process requires the vacuum system to be onstream 80% of the year.
Although the steam system is equipped with separators and steam traps, some moisture does get through to the ejectors. Moisture freezes when the vacuum is pulled down to 0.5-mm Hg because the pressure is much lower than the vapor pressure of water at the freezing point (4.6-mm Hg). Ice buildup in the throat area of the ejector causes a change in geometry that has an adverse effect on ejector performance (see Fig. I).
The plant tried using heat tracing but it did not work. The only answer has been to have live steam contacting the outside of the ejector throat.
Live Steam Effective, But Messy: The plant tried using heat tracing (tubing wrapped around the ejector throat and insulation) but it did not work. The only answer has been to have live steam contacting the outside of the ejector throat. A steam line is arranged so that a number of small nozzles direct and maintain live steam on the diffuser surface.
Freezing weather compounds the problems associated with using live steam to heat the exterior wall of the ejector. Condensation leads to ice formation which is untidy and a potential safety problem. Plant engineers want the steam source enclosed to provide a safer, more tidy installation.
Steam Jacket Stops Icing: Another high-vacuum column in the plant has an ejector with a steam-jacketed throat (Fig. 2). A slight flow of low-pressure · steam through the jacket keeps the ejector wall above freezing and eliminates the hmnation of icc in the throat area.
The ejector manufacturer suggested Philtex install a low-pressure steam jacket to the diffuser area of the first-stage ejector. The new steam jacket eliminates the untidy conditions and noise caused by direct steam and assures continued stable performance by the ejector.
Steam Jet Ejector Vacuum System- Croll Reynolds Co., Inc., NJ.
Plant Profile: Philtex is a specialty chemicals plant that is part of the Phillips Petroleum Co., Borger Complex, located in Borger. TX. A range of products are produced at the facility, such as mercaptans, racing fuels, rocket fuel binders and highly specialized solvents. Philtex currently manufactures a solvent used in AIDS research.
Robert Stitzel, Plant Mechanical Engineer,
Phillips Petroleum Co., Borger Complex Philtex/Ryton Plant
Alan E. Hodel, Senior Technical Editor
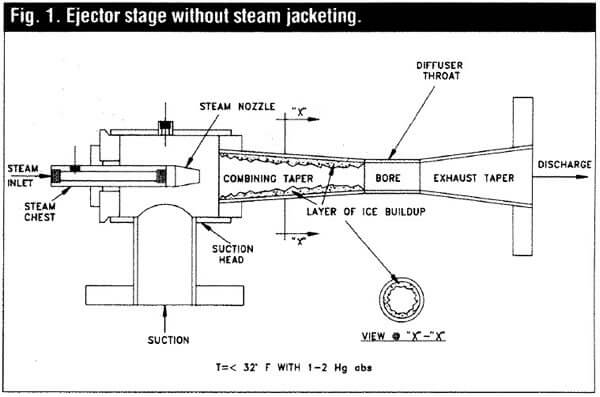
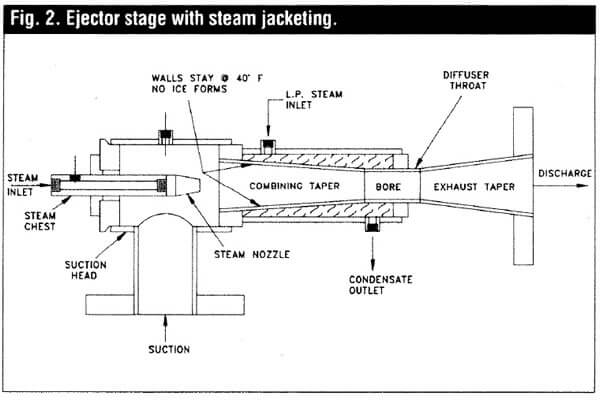
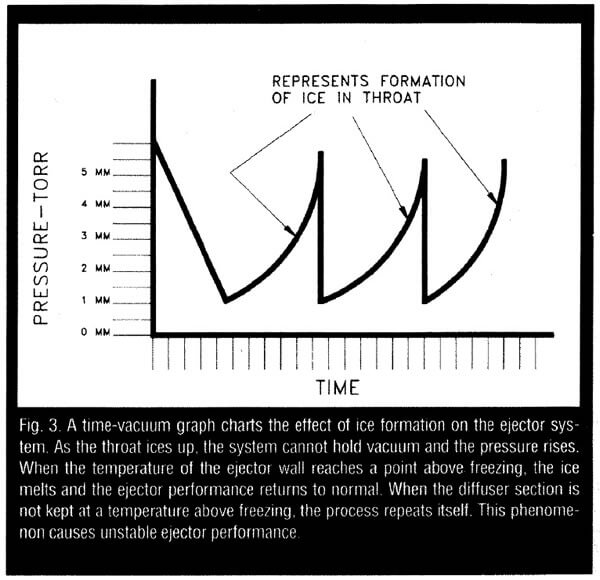