Circulators
Circulators
Uniform mixing and continuous agitation in standing tanks
About
Circulators are a type of jet-mixer that is submerged in a fluid to perform blending actions in open or closed tanks. By keeping tank contents in continuous motion, circulators prevent the stratification of liquids or settling of particles and support uniform liquid characteristics such as density or concentration. Circulators are used to homogenize liquid mixtures, keep solid particulates in suspension, and aerate mixtures at desired turnover rates. Circulators can handle liquids across a range of viscosities and densities and can be utilized in any environment where liquids are stored and handled.
Advantages
- Can utilize a range of motive fluid compositions
- Consistent performance
- No moving parts, no lubricants required
- Low initial cost (compared to mechanical circulator pumps)
- Open construction, easy to install and maintain
- No special pipe supporting required
- Easy to retrofit or upgrade
- Long lasting and durable equipment
- Wide flow variation
- Quiet operation
- Low pressure loss
- Can be constructed from a wide variety of materials
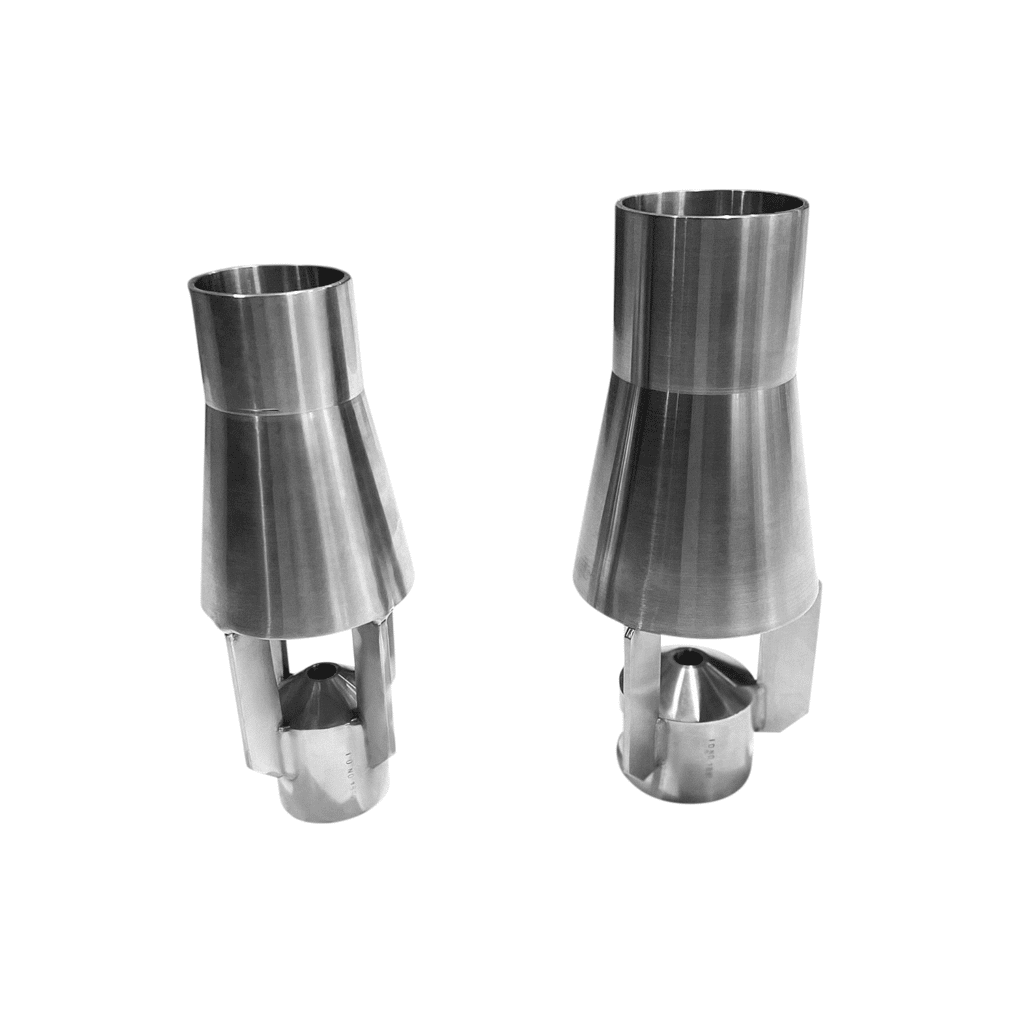
How it works
Eductors and circulators operate on many of the same basic principles, although their construction differs significantly. Circulators are built with an open construction entrainment area and three inlet ports, unlike eductors and ejectors, which have a closed body and a single suction inlet.
Once submerged in a tank’s fluid, circulators are fed a pressurized motive fluid, normally sourced by a small circulator pump for boiler recirculating a portion of the tank’s contents. Mixing is achieved by the high-pressure motive liquid passing through the converging motive jet mixer nozzle at a high velocity, creating momentum to entrain the surrounding liquid through an open suction area in the open construction “body” of the circulator; this results in a discharge plume of liquid which widens as it moves away from its source. This jet mixing plume usually transitions from laminar to turbulent flow, achieving the necessary jet mixing and homogenizing required.
The circulating/mixing efficiency of a Croll-Reynold’s circulator depends on both the differential pressure of jet mixing streams and the circulator’s position in the vessel and angle of the discharge. Multiple circulator units can be used simultaneously depending on tank size, shape and required turnover time. With multiple jet mixer units, the overlapping plumes minimize areas of stagnation.
Once submerged in a tank’s fluid, circulators are fed a pressurized motive fluid, normally sourced by a small circulator pump for boiler recirculating a portion of the tank’s contents. Mixing is achieved by the high-pressure motive liquid passing through the converging motive jet mixer nozzle at a high velocity, creating momentum to entrain the surrounding liquid through an open suction area in the open construction “body” of the circulator; this results in a discharge plume of liquid which widens as it moves away from its source. This jet mixing plume usually transitions from laminar to turbulent flow, achieving the necessary jet mixing and homogenizing required.
The circulating/mixing efficiency of a Croll-Reynold’s circulator depends on both the differential pressure of jet mixing streams and the circulator’s position in the vessel and angle of the discharge. Multiple circulator units can be used simultaneously depending on tank size, shape and required turnover time. With multiple jet mixer units, the overlapping plumes minimize areas of stagnation.
Use cases
- Chemical –product distillation, drying, flash cooling and more
- Oil and Gas – refinery processes, product distillation and more
- Steel – refinery processes, product degassing and more
- Edible Oil – refinery processes, product degassing and more