Kalama Chemical, Inc. (Kalama, Wash.) produces fine and specialty chemicals for chemical intermediates, corrosion inhibitors, food preservatives and flavors. Its flavor and fragrance products are especially heat sensitive, so distillation separations must be carried out at high vacuum.
In 1989, Kalama began manufacturing a new floral fragrance – amyl cinnamic aldehyde. During a typical batch distillation, some components in the stillpot have boiling points very close to the end product’s boiling point, so long purification cycles at high reflux ratios are required for adequate separation.
The lower boiling point achieved by operating the distillation unit at reduced pressures is critical to prevent thermal breakdown. When the firm constructed the distillation facility for this newly developed, specialty chemical, it needed to produce a vacuum of at least 10 Torr, to keep the product from overheating.
The existing liquid-ring vacuum pump in use on Kalama’s distillation system was able to produce a vacuum of only 100 Torr. For amyl cinnamic aldehyde, this would have resulted in a stilpot temperature well above the product’s decomposition temperature.
Maximizing Yield
To achieve the 10 Torr or less vacuum required, Kalama selected a Rotajector vacuum system from Croll Reynolds Co. It consists of two steam ejectors operated in series, followed by a surface condenser (to condense steam from the ejectors) and a liquid-ring vacuum pump (to discharge non-condensable vapors to atmosphere). The hybrid vacuum systems it selected easily produces a vacuum to 2 Torr, using two steam ejectors, a condenser and a liquid-ring vacuum pump.
While the ejector stages produce the high vacuum required, the liquid-ring vacuum pump reduces overall steam consumption. The condensate is used to provide the liquid seal needed for the vacuum pump, thereby greatly reducing the amount of water leaving the system.
The hybrid vacuum system requires only 300 lb/h of 100 lb/ per sqare inch steam, plus the electricity needed to operate the 10hp vacuum pump. During startup, the system evacuates the 400 ft cubed distillation system down to 2 Torr in less than 30 minutes. Using condenser inlet water at 80 degrees F, the 2 Torr vacuum can be maintained, while evacuating the equivalent of 5 lb/h of non-condensible air.
The entire system was pre-assembled by Croll Reynolds, and it arrived at Kalama as a completely piped, skid-mounted unit. The system’s only moving part – the impeller of the liquid ring vacuum pump-makes no metal-to-metal contact with the casing.
Adjust As Needed
These hybrid vacuum systems can use either one-or-two stage vacuum pumps, one or more ejector stages, and optional condensers. To produce vacuum down to 30 Torr, one-or-two stage liquid ring pumps are usually the most economical systems. For greater vacuums, one or more stages of steam ejectors are typically added upstream of the pump.
When steam ejectors are used, a surface condenser placed immediately upstream of the pump minimizes the required pump size, by cutting the condensible vapor load. In the five years since Kalama installed the Rotajector system in it’s amyl cinnamic aldehyde line, the firm has installed two additional Rotajector systems for other flavor and fragrance products.
Edited By: Suzanne Shelley
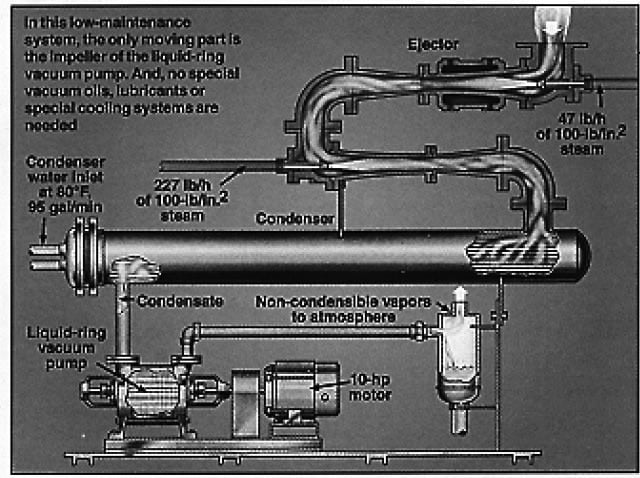