Refinery Vacuum System
Refinery Vacuum System
Vacuum distillation for hydrocarbon recovery and processing
About
Croll Reynolds vacuum systems are a low cost and efficient solution for the vacuum distillation application. Vacuum distillation is a common method to separate mixture components under reduced pressure. Vacuum distillation is mostly utilized to allow lower boiling point compounds to separate from higher boiling point compounds in the mixture introduced in a vacuum tower. Refineries are one of the main areas where Croll Reynolds vacuum system helps the process of distillation to extract and capture light hydrocarbons that disassociate from crude oil, which helps avoiding problems such as thermal degrading or discoloration of the products.
Around 70% of the refineries across the world utilize vacuum distillation unit (VDU), after using atmospheric distillation unit (ADU) from where the bottoms are sent to VDU unit and increase the production of high-value petroleum products. Croll Reynolds Ejector vacuum systems offer a reliable and economical means of handling and compressing large flows of light hydrocarbons our of Vacuum distillation tower from designed vacuum level to desired back pressure in the main condensate drum, where sour condensate water separates from slop oils.
Advantages
These are the primary advantages of installing ejectors versus mechanical pumps for high-volume, low-pressure applications.
- Lower operating costs
- Prevents hydrocarbon chains from breaking from undue, excessive heat
- Reduces other undesirable secondary reactions
-
Increases product recovery
(under maximum temperature constraints) - Reliable, consistent service and output
- No moving parts
- Low initial cost (compared to mechanical pumps)
- Minimal maintenance cost (compared to mechanical pump)
- Easy to operate and maintain
- Easy to retrofit or upgrade
- Long lasting and durable equipment
- Can be constructed from a wide variety of steel, alloy, high alloy, including corrosion resistant coatings of all components.
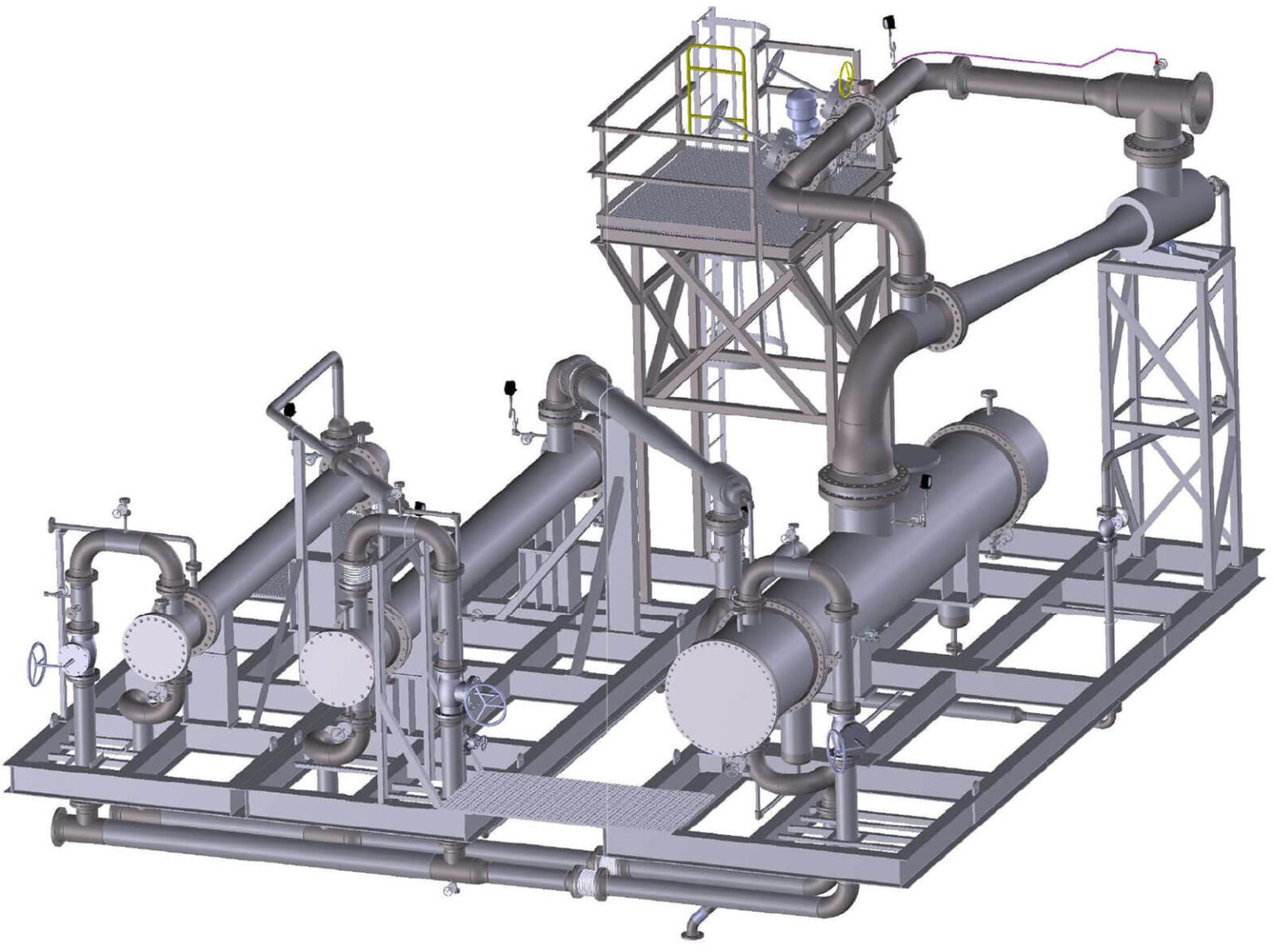
Vacuum distillation columns utilize vacuum system to achieve absolute pressure of 8 to 40 mmHg in the column using 2 to 4 stages of steam jet ejectors or a combination of steam ejectors and liquid ring vacuum pumps (Hybrid Ejector Vacuum System). The vacuum created in the column will be handled by usually large size 1st stage ejector, arranged with minimal interconnecting piping to reduce the pressure drop between the column and the vacuum system. Usually, the optimal number of stages for VDU systems with low-medium back pressure (≤ 0.3 bar G) are 3-stages of ejectors and condensers. The low pressure generated in the column will provide good vapor-liquid contact and achieve necessary pressure drop for the column. The vapor moving through the column condenses in distillation trays and then are withdrawn from the side of the column. For VDU systems with back pressure ≥ 0.3 bar G the system will be more efficient with 2 to 3 stage of steam jet ejectors with the addition of liquid ring vacuum pumps overcoming the high back pressures (up to 0.8 to 1.0 bar G).
- Oil and Gas – refinery processes, product distillation and more