Oil & Gas
Oil & Gas
Croll Reynolds Co., Inc.is a leading manufacturer of vacuum systems and heat recovery systems have multiple applications across various industries in the Energy sector. The Oil & Gas industry relies on our advanced systems to perform vacuum distillation; the primary process used to petroleum and other alcohol-based products.
Our vacuum and hybrid ejector-liquid ring systems are installed in numerous refineries worldwide, primarily in the Middle East, Asia, Europe, and the United States. We have meticulously engineered our products to operate with exceptional efficiency in demanding environments, ensuring optimal processing performance and precision resource handling at-scale.
What is Vacuum Distillation in the Oil & Gas Industry?
Vacuum distillation is essential in refining, where heavier oils are fractionated to produce petroleum products. Almost all oil & gas refineries in the United States use vacuum distillation units or “VDU” in their process.
First, an initial atmospheric distillation process lays the groundwork for a VDU by separating lighter hydrocarbons from heavier oils. During the secondary vacuum distillation process, the heavier oils undergo further refinement to yield high-value petroleum products These products include:
- Kerosene
- Jet fuel
- Diesel
- Naptha
- Gasoline
- Light-cycle oil
A superior-quality vacuum ejector is required to enhance or improve a refinery’s refining process. Fortunately, our expert engineers design and develop products that undergo stringent manufacturing processes and adhere to strict quality controls. The systems we develop are also extensively tested and analyzed in-house to ensure they meet HEI requirements, and other criteria governing particular application designs.
A Vacuum Ejector System’s Role in Refineries
A reliable and well made ejector presents plenty of advantages across refinery process stages. Ejector systems are composed of condensers and ejectors that are arranged in series. Together, they create and maintain sub-atmospheric pressure inside the distillation column to allow the fractionation of heavy crude oils into various components to reduce the lower-value residuum. Ejector-based vacuum distillation systems allow for greater yields of quality gas, oil and other valuable petrochemical byproducts.
Benefits of high-performance ejectors:
- Ejectors are effective and easy to operate
- Energy efficient without compromising product quality
- Increase in yield and profitability
- Minimal annual maintenance requirements
Selecting the Appropriate Ejector System
Our team possesses comprehensive knowledge of various ejector technologies available, enabling us to offer a wide range of custom superior vacuum systems. Since there are several types of ejector systems, choosing the right one for your vacuum distillation equipment will depend on the vacuum level requirement in the column, material requirements, and various modes of operation including turndowns and upset cases. Creating a system that is suited to handle such cases involves designing major components while taking into account all automated valves, instrumentations, interconnecting pipes and piping elements t, all of which are routinely handled by our seasoned team of experts and engineers at Croll Reynolds.
Heat Recovery in the Oil & Gas Sector
Heat recovery pertains to recapturing and reusing energy from steam used within various oil and gas sector operations. Heat as energy can be recovered by thermocompressors and other recovery technologies that recycle heat and reduce energy consumption.
A thermocompressor works to effectively compress a low-pressure fluid to an intermediate pressure. The recompressed fluid’s heat value is then reclaimed for other use-purpose within a parallel, upstream, or downstream process. Oftentimes, the recompressed fluid itself is also reintroduced back into the system as an additional energy source somewhere within the site operations
Minimizing Operating Costs through Heat Recovery
Recycling heat from exhaust gases significantly reduces operating costs for companies. At Croll Reynolds Co., Inc., we specialize in providing comprehensive solutions that streamline operations and enhance system efficiency. Our products can be seamlessly integrated with existing facility systems, offering a cost-effective approach to heat recovery.
Choose Croll-Reynolds Co. for Exceptional Oil Refinery & Heat Recovery Systems
At Croll Reynolds, we have developed cutting-edge vacuum distillation ejector systems and heat recovery systems well-tailored to the specific needs of the Refinery, Oil, and Gas sector. We possess over a century’s worth of in-depth knowledge of industry requirements while remaining committed to delivering exceptional customer service from start to finish.
If you have any questions about our products, don’t hesitate to contact us or request a quote and we’ll find a solution to deliver customer success.
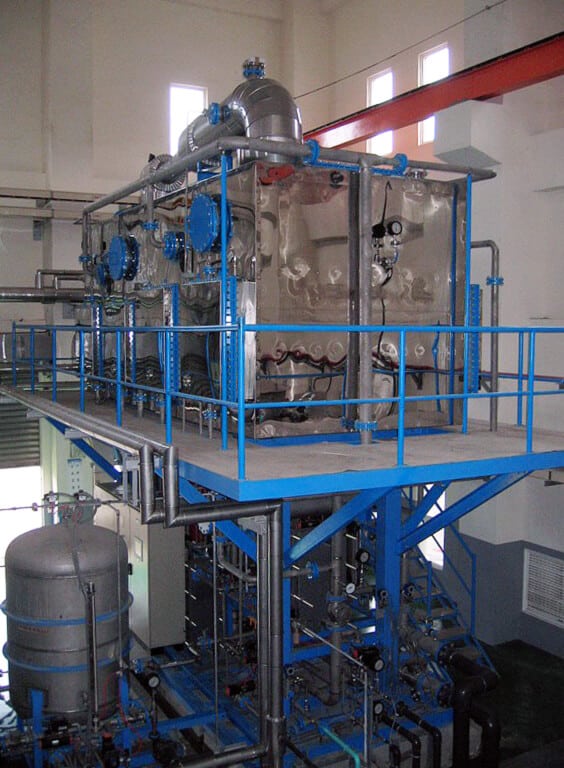
Efficiently Recycling Heat Energy
Croll Reynolds has been involved in heat recovery since the 1940s when our Thermocompressors were first used by the US food and dairy industries to recapture and recompress spent steam from multi-effect evaporators. The applications for thermocompressors continue to expand as process engineers in the petroleum, chemical, power, food and paper industries find areas of plant operations where the energy from steam can be recaptured and reused.
The ejector is applied to produce vacuum . The thermocompressor is designed to entrain and compress a low pressure fluid to an intermediate pressure. The heat value of the recompressed fluid, commonly steam, can then be reclaimed and reused elsewhere.
The advantage of the thermocompressor vs a mechanical compressors is the absence of moving parts, low maintainance costs and very low capital cost.
Mechanical design:
The mechanical design of the thermocompressor is similar to that of the steam ejector. Like the ejector, a thermocompressor consists of four component parts , the nozzle holder, nozzle, steam chest and diffuser. Thermocompressors are designed in single, multiple, or adjustable nozzle configurations depending on the application.
Operation:
Like an ejector, the thermocompressor uses a high pressure steam as a motive fluid. The motive fluid is piped into a steam chest and expands through a converging-diverging nozzle. This high velocity stream entrains the steam entering the suction inlet and the mixed fluids are then compressed to an intermediate pressure as they pass through the diffuser ( throat ). The diffuser acts as a nozzle in reverse, reconverting velocity energy to pressure energy.
Case Studies
Plant Maintenance
Featured Products
refinery processes, product distillation and more
product distillation with high pressure fuel gas, heat recycling of exhaust gasses, and more
refinery processes, product distillation and more
product distillation with high pressure fuel gas, heat recycling of exhaust gasses, and more
refinery processes, product distillation and more
boiler heat recovery systems and more
heat recycling from exhaust gasses and more
heating fluids in tanks and pipelines for various processes
draining and transport of liquid byproducts and more